Enterprise Software House specializes in custom MRO software integrations, ensuring that airlines have a seamless, data-driven approach to maintenance operations. By developing tailored integrations that unify maintenance management, operational data, and predictive analytics, we help airlines reduce downtime, improve asset utilization, and enhance regulatory compliance.
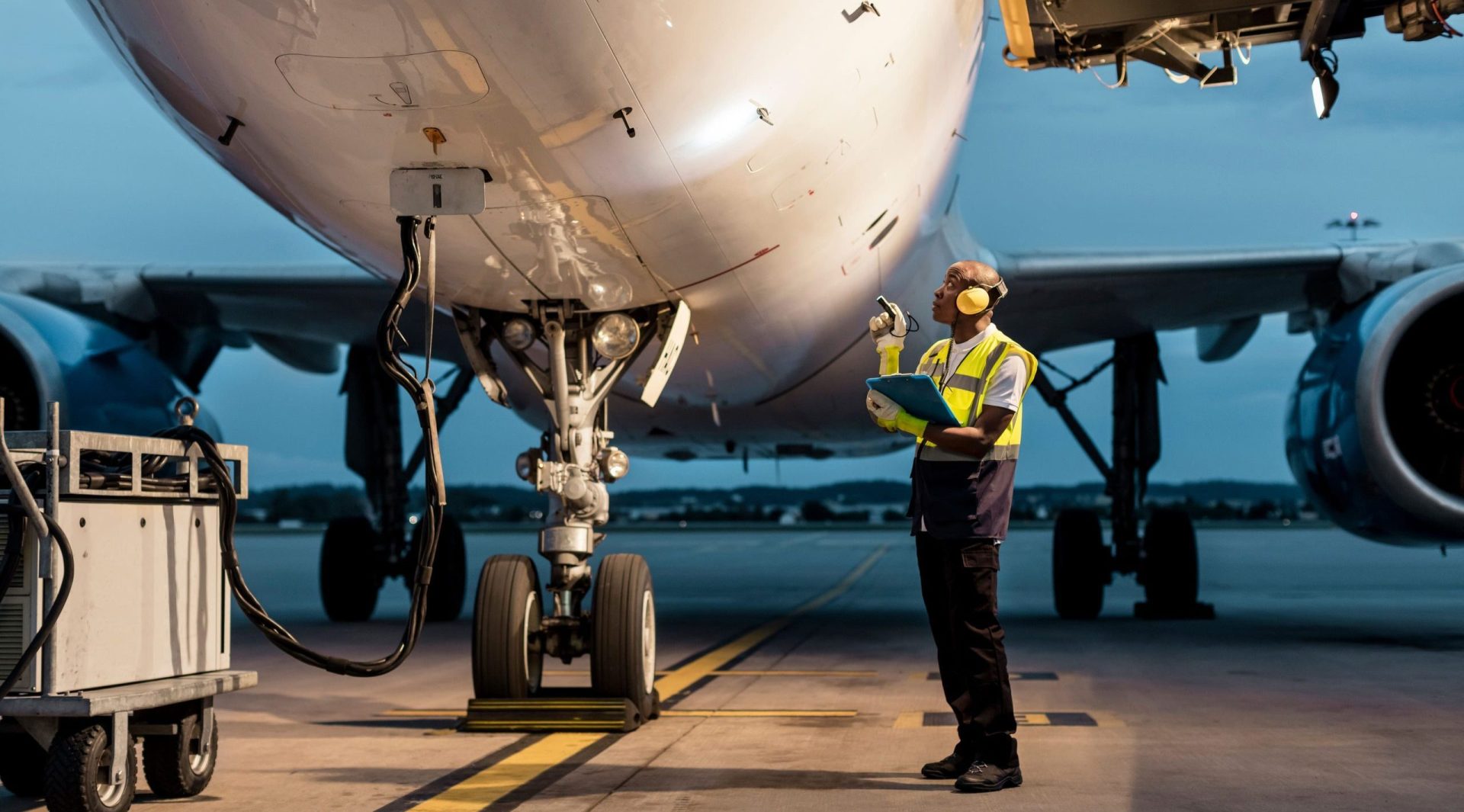
Optimizing airline maintenance with software integrations
Aircraft maintenance is one of the most critical aspects of operations, directly impacting safety, compliance, and efficiency in aviation. However, many airlines struggle with fragmented IT environments, outdated legacy systems, and disconnected workflows, leading to delays, increased operational costs, and compliance risks.
Aircraft maintenance is one of the most critical aspects of operations, directly impacting safety, compliance, and efficiency in aviation. However, many airlines struggle with fragmented IT environments, outdated legacy systems, and disconnected workflows, leading to delays, increased operational costs, and compliance risks.
Eliminating data silos for real-time maintenance efficiency
One of the biggest challenges airlines face is data fragmentation. Maintenance teams often rely on multiple systems for engineering, inventory, compliance, and flight operations, but these systems don’t always communicate efficiently. As a result, technicians spend unnecessary time manually entering data, retrieving maintenance histories, and ensuring regulatory paperwork is in order.
We develop custom solutions that integrate different maintenance and operational software.
This allows airlines to:
- Automatically synchronize maintenance logs across engineering, inventory, and compliance platforms
- Eliminate manual data entry errors by ensuring seamless communication between different applications
- Enable real-time access to aircraft health data, so maintenance teams can make faster, data-driven decisions
CASE STUDY
A large aircraft maintenance company manages an extensive inventory of parts, each accompanied by a vast amount of documentation. They store part-related data for various airlines in their centralized maintenance system application, manually recording every detail, from origin and condition to installation history. However, out client (MRO company, part of national aviation group) requires the same data to be entered into their airline-specific maintenance platform system, leading to duplicate manual work. This redundancy slows down operations and increases the risk of errors. To address this, we proposed an automation solution using a bot to enter data into both systems simultaneously or at least transfer it from one system to another. This approach reduces manual effort, enhances data accuracy, and improves overall efficiency.
Automating maintenance workflows for faster turnarounds
Aircraft maintenance involves multiple stakeholders e.g. technicians, engineers, procurement teams, and regulatory bodies. Without a streamlined digital workflow, approvals and documentation can delay maintenance tasks.
We build custom digital workflow automation that:
- Automates work order creation based on predefined rules and real-time triggers.
- Connects technicians with digital maintenance records via mobile interfaces.
- Enables instant approvals for parts procurement and work completion.
CASE STUDY
The same airline struggled with paper-based maintenance logs and slow approvals for part replacements. We implemented a cloud-based workflow system that automatically updated records and sent real-time alerts to relevant teams. This reduced approval times and improved aircraft turnaround rates.
Ensuring regulatory compliance with digital audit trails
Compliance with aviation safety regulations requires airlines to maintain meticulous records of maintenance activities, component changes, and inspections. Manual documentation processes often lead to errors, lost records, and compliance risks.
We develop digital compliance solutions that:
- Automatically generate maintenance reports in line with aviation regulatory standards.
- Ensure all maintenance activities are digitally logged and traceable.
- Provide auditors with instant access to historical maintenance data, reducing compliance risks.
USAGE EXAMPLE
Client facing repeated challenges in preparing for aviation audits. Our automated compliance tracking system can ensure that all maintenance logs were digitally recorded and instantly retrievable, reducing audit preparation time.
Optimizing spare parts inventory with smart integrations
A common issue in MRO operations is poor spare parts inventory management, which can lead to maintenance delays when parts are unavailable. At the same time, overstocking spare parts increases costs.
We integrate real-time inventory tracking with maintenance scheduling to:
- Predict part demand based on upcoming maintenance needs and past failure rates.
- Automatically reorder critical components when stock levels drop.
- Improve visibility across multiple maintenance hubs, ensuring the right parts are available at the right location.
USAGE EXAMPLE
An airline struggling with frequent part shortages and delays. By implementing a smart inventory forecasting system, we can reduce out-of-stock situations, ensuring smoother maintenance operations.
Enterprise Software House - airline maintenance with smarter integrations
By eliminating data silos, leveraging real-time monitoring, automating workflows, ensuring regulatory compliance, and optimizing inventory, airlines can significantly reduce operational costs, minimize downtime, and enhance safety.
At Enterprise Software House, we specialize in custom software solutions tailored to the unique needs of the aviation industry. Whether it’s integrating existing systems, developing predictive maintenance capabilities, or automating workflows, our expertise ensures that your airline operates more efficiently and with fewer disruptions. Contact us through the form below and let’s talk about how we can help you in achieving better results.